Protipožární nástřikové hmoty ve stavebnictví
Publikováno dne 4. 11. 2009
Autor: Eduard Vašátko
S vyjímkou deskových silikátových obkladů jsou protipožární nástřikové hmoty jedním z prvních ochranných systémů, které se ve stavebnictví používaly již v šerém dávnověku. Nejstarším takovým materiálem byl jíl a hliněné omítky, kterými byly chráněny dřevěné a rákosové stěny stavebních objektů a které se v mnoha zemích užívají dodnes, i když samozřejmě ne jenom jako ochrana proti požáru. Ke zvýšení požární odolnosti pak celá staletí sloužily i všechny vápenné i cementové omítky, ať již bez výztuže nebo i vyztužené např. rákosem či jinými materiály. Všechny tyto materiály však měly své limity, jejich parametry odpovídaly většinou dnešním omítkám skup. III a jejich tepelně izolační vlastnosti byly poměrně nízké. Ostatně – i dnes má smysl používání omítek v protipožární ochraně ( bez ohledu na zatřídění) až od tloušťky 10 mm a více. Přesto, že státní i městské úřady do jisté míry upravovaly i podmínky pro stavby a již v 17. století existovaly nejrůznější požární řády a nařízení pro konstrukci a dislokaci staveb z tohoto hlediska, byla protipožární ochrana jednotlivých objektů řešena téměř vždy individuálně. (Krásné bronzové nádoby o obsahu cca 1 m3 na požární vodu byly např. pravidelně rozmístěny i v císařském paláci v „zakázanem městě“ v Pekingu (a jsou tam ostatně dodnes). Fotky mám schované.)
První moderní typy tepelně izolačních omítek a protipožárních nástřikových hmot se u nás objevily již koncem 19. a začátkem 20. století, prakticky žádné bližší údaje se však o nich nezachovaly. Je pravděpodobné, že se jednalo převážně o sádrové omítky a štuky, případně vyztužené pletivem, jejich účinnost se nám však nepodařilo zjistit.
Přesnější informace jsou k dispozici až od 70. let minulého století (hlavně proto, že tohle si už pamatuji – je zajímavé, jak málo údajů o těchto materiálech se zachovalo i v odborné literatuře). Po velkých požárech v Praze a Ostravě a zejména s ohledem na přípravu stavby první moderní jaderné elektrárny v Dukovanech se řada výzkumných pracovišť v celé republice začala intenzivně zabývat vývojem protipožárních hmot a konstrukcí. Vedle toho byly pro potřeby velkých administrativních objektů dovozních společností a dalších budov (KOVO, STROJIMPORT, MOTOKOV, CHEMAPOL, Palác kultury), jejichž výstavba byla v těchto letech zahájena, dováženy i protipožární nástřiky ze zahraničí a některé z nich byly ověřovány i zkouškami v ČR.
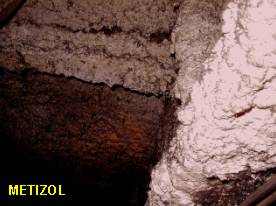
K nejlepším tehdy dováženým nástřikům patřil vermikulitový protipožární nástřik THERMAX(ISOVOLTA Vídeň – nezaměňovat s deskami stejného jména), dovážen byl i nástřik PYROK, jehož výrobní licenci později zakoupilo VD SIAL, anglická firma J.W.Roberts dodávala pro stavbu některých objektů nástřik LIMPET, obsahující až 75 % vláknitého azbestu, pro aplikace byl schválen i nástřik AZBESTOSPRAY. Slovenská firma Prefmonta ověřovala v letech 1978 – 9 vlastní nástřik TERMIZOL,o něco později n.p. Stavokonstrukce Praha přišly na trh s nástřikem UNIPRON, což byla určitá obdoba předchozího PYROKu, ve kterém byl vermikulit nahrazen experlitem. Stavební izolace Praha nabídly k aplikaci obdobný nástřik, obsahující minerální vlákno pod názvem METIZOL P. Velmi dobře propracovaný byl i slovenský nástřik SIBATERM, vyráběný a aplikovaný až cca do roku 1992 firmou Stavoindustria, Bratislava. Je třeba se zmínit i dováženém maďarském nástřiku Polystop K – Poliplast, který k nám byl dovážen přibližně ve stejných letech maďarskou firmou Dunamenti.
Lze konstatovat, že většina těchto nástřiků dosáhla pouze malého rozšíření a od jejich používání bylo postupně upuštěno. Pro dovážené nástřiky nebyly k disposici devizové prostředky, mimo to bylo v pozdějších letech omezeno a nakonec zcela zakázáno používání nástřiků na bázi azbestu, nástřiky čs. provenience bylo nutno dostatečně odzkoušet a ne každý výrobce měl dostatek času a peněz, aby dořešil celou potřebnou dokumentaci. Řada nástřiků zmizela z trhu, když zanikl jejich výrobce v poslední dekádě minulého století.
Na trhu se proto dodnes udrželo pouze několik systémů, které byly dostatečně propracovány a které dodnes snesou náročná měřítka průběžně se zpřísňujících norem a požadavků.
Výskumný ústav stavební v Košicích vyvinul v letech 1976 – 8 protipožární nástřik, kde bylo užito sádry jako pojiva pod obchodním názvem PYROTHERM. Tento nástřik byl průkazně odzkoušen na ocelové konstrukce a je dosud jediným nástřikem na této bázi, který se u nás používá. I když mám k jeho aplikaci určité výhrady, lze konstatovat, že v případě, kdy je přesně dodržena správná aplikační technologie, jde o velmi kvalitní a účinný systém.
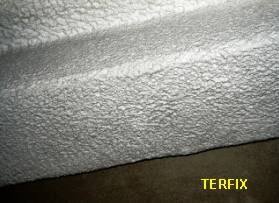
V letech 1972 až 4 byl v rámci výzkumného úkolu VVÚSZ v Praze Malešicich zahájen vývoj prvního skutečně moderního protipožárního nástřikového systému na vápenocementové bázi pod názvem PORFIX. Tento nástřik se – po dořešení aplikační technologie a zejména konstrukce stříkacího zařízení a po dokončení komplexních zkoušek požární odolnosti zejména v ČR velmi rychle ujal, hlavně proto, že byl včas nalezen i vhodný výrobce, což v plánovaném socialistickém hospodářství nebylo právě snadné. PORFIX byl potom základem pro další zlepšování funkce a aplikačních vlastností a v průběhu několika let (1980) se objevila zlepšená varianta pod názvem TERFIX TCVV 800/400. Je zajímavé, že se používají dodnes obě varianty vedle sebe. Posledním stupněm v této vývojové řadě je dále zlepšený nástřik TERFIX/TERMO PS a jeho úpravy v podobě koncentrátů.
Současný sortiment na českém trhu doplňuje poslední výrobek, průkazně odzkoušený v minulém roce a vyvinutý brněnským VUSH pod názvem UNIMIX POO. Nástřik je formulován na bázi vermikulitu a lze očekávat, že po dořešení některých technologických problémů s aplikací jistě nalezne s ohledem na své velmi dobré vlastnosti své uplatnění, především pro ochranu OK.
Zajímavou kuriozitou byl protipožární nástřik na bázi vodního skla, který se objevil na Slovensku přibližně v letech 1994 – 5 pod obchodním označením TAHIZOL. Tento nástřik s velmi dobrými funkčními i fyzikálně mechanickými vlastnostmi byl dokonce dvakrát za sebou úspěšně odzkoušen ve zkušebně PAVUS – Veselí n.L. a údajně měla být v Bratislavě zahájena i jeho výroba (předpokládanou výrobnu jsem viděl na vlastní oči), bohužel – na trhu se podle mých informací vůbec neobjevil a jak rychle se objevil, tak rychle zmizel. Zajímavé na něm bylo především to, že při požáru vytvářel velmi rychle tvrdou, dobře tepelně izolující pěnu a jeho objem se během zkoušky zvětšil až 10 x. Sám jsem byl oběma zkouškám přítomen a viděl jsem nosníky po zkouškách, které byly kolem dokola obaleny hmotou, připomínající porobeton. Ať již byl další osud tohoto materiálu jakýkoliv, je zřejmé, že nástřikové protipožární hmoty mají před sebou ještě značnou budoucnost.
Za zmínku stojí i orientační zkoušky materiálu CLIMATIZER PLUS v roce 1997 na dřevěných deskách. Vzhledem k organické bázi tohoto tepelně izolačního materiálu by bylo nutno provést zřejmě ještě řadu úprav, chování vzorků však naznačuje, že by bylo možno i tento systém časem využít, zejména s ohledem na jeho nízkou hmotnost alespoň pro některé specifické konstrukce.
Závěrem k tomuto spíše historickému přehledu ještě alespoň základní rozdělení protipožárních nástřiků z hlediska jejich složení:
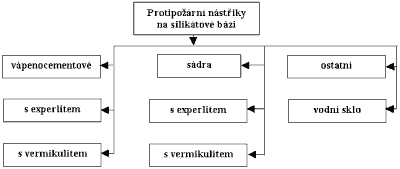
A protože další referát (Protipožární nástřiky a omítky) již bude zaměřen výrobkově a je zpracován odborníkem, který se těmto hmotám podstatnou část života věnoval (a proto nemůže být zcela objektivní ve vztahu k ostatním protipožárním systémům – jak známo,“každá liška svůj ocas chválí“ , což mu samozřejmě nemohu mít za zlé) dovolím si ještě stručně zhodnotit výhody a nevýhody jednotlivých nástřikových systémů sám.Proto mohou být mezi mým hodnocením a následujícím referátem určité rozdíly, které – jak pevně věřím – sami posoudíte.
Co se vlastně od nástřiků požaduje a jaké jsou rozdíly v aplikaci ve srovnání s intumescentními nátěry ?
Na rozdíl od protipožárních nátěrů mají nástřiky nesrovnatelně horší vzhled a nelze je použít do běžného interiéru. Jejich povrch je nerovný a až na vyjímky je nelze hladit (resp. dnešní systémy to umožňují, ale povrchová úprava je dosti nákladná), dodatečná povrchová úprava je značně náročná a dosti nákladná. Jejich objemová hmotnost je proti nátěrům mnohonásobně vyšší, více zatěžují konstrukci, problematická je v řadě případů i jejich adheze k povrchu, zejména u železobetonových prvků z kvalitnějších hutněných nebo propařovaných betonů (Nepříjemné je, že k odpadávání nástřiků může dojít až po určité době – někdy i za několik let, kdy už je po garanční lhůtě a hlavně – kdy už se nástřik mokrou cestou opravuje velmi těžko). V čistých provozech může být na závadu značně velký povrch nástřiku (vzhledem k nerovnostem), což může mít za následek usazování prachu, který pak lze odstranit jen velmi obtížně. Nástřiky jsou také poměrně křehké a nesnášejí dynamické namáhání konstrukce. To vše musí mít projektant na paměti, pokud se rozhodne navrhnout jejich aplikaci.
Oproti nátěrům však nástřiky nabízejí řadu výhod. Nástřiky umožňují zajistit většině ocelových, někdy i železobetonových nosných konstrukcích prakticky všechny požadavky, kladené projektovými normami, tedy od 15 až do 180 minut, jsou při správné aplikaci a vhodném prostředí stálé a stárnou jen velmi pomalu, což znamená, že jejich parametry zůstávají zachovány dlouhodobě. Na konstrukci nastříkaná vrstva dosahuje po dokončení a vysušení prakticky všech svých vlastností ihned a nikoliv – jako u nátěrů – až při požáru. To také znamená, že nemůže dojít k ovlivnění jejich tepelně izolační funkce jakýmikoliv dalšími změnami konstrukce, dodatečnými obklady nebo jinými úpravami a proto se dá požární odolnost nastříkané konstrukce a následných protipožárních úprav téměř vždy sčítat. Neposlední výhodou jsou ve srovnání s nátěry i výrazně nižší náklady na dosažení požadované požární odolnosti, což se rozhodně o nátěrech říci nedá, zvláště, pokud se do nákladů zahrne i životnost. Důvodů pro jejich využití je tedy poměrně dost.
Jejich funkce při požáru je dána jejich složením. Jak vyplývá z předchozího schématu, jedná se vesměs o silikátové hmoty, obsahující obvykle lehčené složky s vysokým obsahem vzduchu, případně doplněné o další plniva, zlepšující tepelně izolační vlastnosti. Podmínkou je, aby všechny základní použité materiály odolávaly co nejdéle vysokým teplotám a zůstávaly dlouhodobě stabilní i při běžných provozních podmínkách. Dalším požadavkem je dobrá adheze k podkladu, odolnost proti agresivnímu prostředí a průmyslovým atmosférám, nízká hmotnost a co nejlepší fyzikálně-mechanické vlastnosti. Požadavků tedy není málo a téměř žádný z nabízeného sortimentu nástřiků není schopen vyhovět všemu, každé materiálové provedení má své výhody a nevýhody:
Mezi nejlepší a technicky nejvýhodnější lze řadit protipožární nástřiky na bázi vermikulitu s přídavkem cementu a vápenného hydrátu. V posledních letech jsou do směsi přidávány i některé typy akrylátových disperzí. S ohledem na obsah vermikulitu mají tyto nástřiky velmi dobré tepelně izolační vlastnosti, což se projevuje nižšími požadavky na výslednou tloušťku ochranné vrstvy. Náklady na tento typ nástřiků bývají obvykle vyšší, úspory lze však dosáhnout jednak nižší spotřebou hmoty a v důsledku toho nižší pracností.
Srovnatelné a z hlediska funkce jen mírně horší jsou nástřiky obsahující stejné pojivo a expandovaný perlit. Pro dosažení stejné požární odolnosti je sice zapotřebí silnějších vrstev hmoty a výsledný nástřik má mírně horší fyzikálně-mechanické vlastnosti, naopak jsou materiálově levnější.
Nástřiky na bázi hydrátu síranu vápenatého, jinak řečeno sádrové nástřiky, ať již s vermikulitem či experlitem jsou z funkčního hlediska velmi dobré a plně srovnatelné s předchozími. Jejich výhodou je navíc to, že při teplotách nad 100oC se ze sádry uvolňuje velké množství chemicky vázané i volné vody, která snižuje v prvních fázích teplotu plamene a zpomaluje ohřívání nastříkané vrstvy. Naopak podstatnou nevýhodou sádry jako pojiva jsou značné objemové změny při vyšších teplotách, způsobené právě ztrátou vody. Tyto objemové změny mají za následek jednak vznik trhlin v nástřiku, jednak se mohou postupně oddělovat i jednotlivé stříkané vrstvy od sebe. I když je možno velkou část těchto změn eliminovat armováním stříkané směsi anorganickými vlákny, zůstává použití těchto typů nástřiků z tohoto hlediska přímo závislé na přesné práci a přesném dodržování výrobní technologie,kde záleží na dodržení optimálního stechiometrického poměru vody se sádrou při míchání nástřikové směsi.
Sdílejte článek
Další články v sekci Problematika požární ochrany
- Protipožární nástřiky a omítky
- Vady a problémy aplikace protipožárních nástřiků
- Problematika desek a deskových konstrukcí v protipožární ochraně staveb
- Požární problematika dřevěných konstrukcí
- Kabelové rozvody a instalace v požárně dělících konstrukcích
- Skúška požiarnej odolnosti podľa uhľovodíkovej teplotnej krivky
- Některé chyby a omyly při projektování a aplikaci prostředků, zvyšujících požární odolnost stavebních konstrukcí
- Požární uzávěry a jejich hodnocení podle ČSN EN 1634-1
- Problematika požární ochrany nosných i nenosných ocelových konstrukcí ve stavebnictví
- Příspěvek k požární odolnosti dílců Spiroll